Improving System Reliability in Washdown Environments
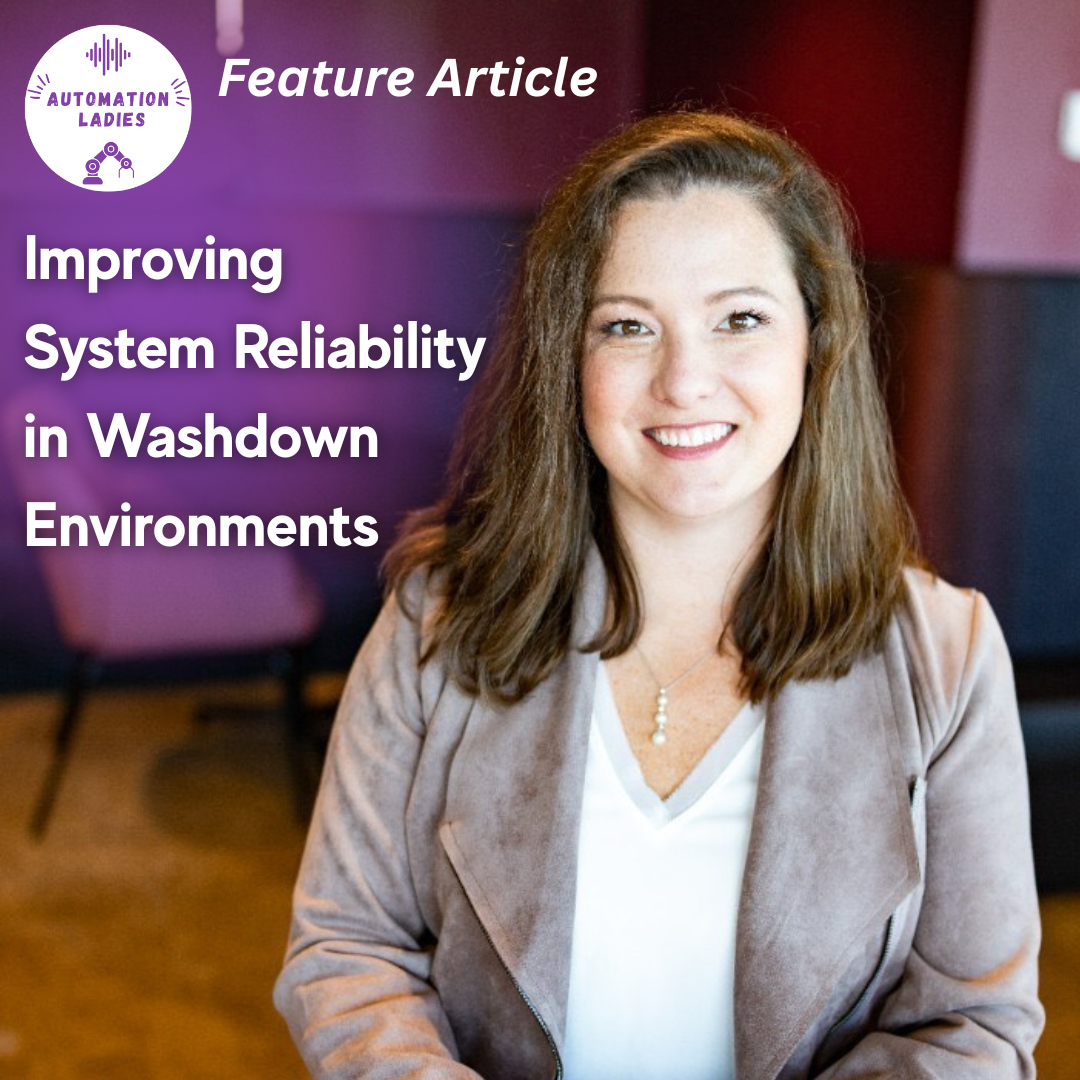
Special Article by Dana Myers, nVent
Properly specifying electrical enclosures designed to endure intense washdown environments is no easy task. Especially in food and beverage applications, where washdown procedures are extremely intense, industrial design engineers must keep a few key factors in mind. To begin, enclosures must be correctly designed and constructed of robust, high-quality components that help keep food product and consumers safe from contaminants throughout operations. However, that is just the beginning.
Food and beverage manufacturing environments require high-pressure washdowns and harsh cleaning chemicals to maintain sanitary conditions. Successful washdowns remove all waste materials and residue from processing systems and controls. This preserves product quality and consumer safety. Without proper protections, these essential processes can damage enclosures and put the electrical controls contained within them at risk. Even with the appropriate ratings, if electrical and electronic controls are not properly enclosed and protected from undesirable washdown side effects—such as product damage, contamination or corrosion—manufacturers may face significant consequences including production downtime, food product contamination and high equipment replacement costs. Attention to detail in the design process can mitigate challenges down the road.
Intense Washdowns, Critical Designs
In food and beverage environments, workers perform washdown procedures in operating areas at least once per day. Certain parts of the operation may also utilize a clean-in-place (CIP) system: a contained area that is cleaned on a specified schedule using an automated and highly controlled process. Oftentimes, CIP uses harsher chemicals and higher pressure than standard washdown procedures. Enclosures in CIP environments are commonly referred to as “sanitary design,” and this equipment is often assigned to a specific team member at the facility, such as a sanitation engineer.
Skipping critical elements of harsh environment controls design within CIP systems can create premature failures of control systems, downtime events or unsafe work environments. Engineers need to start with three key elements of enclosures design for sanitary environments: the hinge, latch and the gasket. Each requires unique considerations and design elements to support their success.
Hinge
Enclosures hinges provide a secure seal and add security for electrical components. Sloped surfaces, lift-off, bullet-style enclosure door hinges are the best choice for washdown environments. These hinges feature a rounded top and smooth finish to allow complete and easy hinge area cleaning, minimizing entrapment of food product and bacteria. These hinges also allow for easy access to the interior of the enclosure, making it simpler to perform maintenance, inspections and modifications. The highest performing hinges are robust, removable and have durable strength in the face of repeated chemical exposure.
Latch
To keep latches clean and ensure washdowns can effectively remove contaminants, sanitary environment specifiers should consider a low profile (flush with the enclosure) or smooth latching design with a minimal number of openings, such as tool-to-open slots. It is equally important to choose a handle that latches securely and forcefully to prevent washdown solution and harsh cleaning chemicals from entering the enclosure. A latch with a tool-free or easy to use closure is easy and dependable, saving time for workers on the floor.
Gasket
While choosing the optimal enclosure construction and design for washdown is essential, selecting a high-performance seal or gasket is a critical component to ensuring the enclosure’s success. Gaskets and their fixation mechanism or adhesives must be constructed of materials that are compatible with stainless steel, since this is typically the specified enclosure material in these applications. Also, gaskets and adhesives must withstand harsh chemicals during washdowns and be checked periodically for resiliency loss and compression memory. The gasket can be considered the most critical point of design since it protects the enclosures critical automation and control equipment from external elements.
Demystifying Enclosures Ratings for Sanitary Design
In sanitary designs, any concave shape or crevice is considered a potential location to harbor bacteria and potentially difficult to sanitize. The core of sanitary design is to utilize materials of construction and components that are sanitary and can endure harsh chemicals. However, it is also very important to understand and pay attention to what different ratings mean in practice.
4x is a typical rating set by UL for the majority of all corrosive environments for industrial controls. Oftentimes, specifiers will require a type 4x level of equipment protection rating for food and beverage. That is a good start for a low or zero sanitation requirement area, however, this rating overlooks critical elements of sanitary design, including bacteria harboring surface components of an enclosure like crevices, ledges, overhangs or flat-topped surfaces that are seen on common 4x industrial enclosures hinges, latches and gaskets. It is important to consider designs that minimize or eliminate these surfaces even though 4x does not explicitly call for it.
It is also worthwhile to point out that the newly adopted rating of IP69 is not synonymous with sanitary design. IP69 is a high-pressure water ingress protection test procedure that is fully independent of elements of sanitary design. When selecting enclosures, it is important to look for the key elements of sanitary designs outlined in this article, instead of just going by ratings.
About the Author:
Dana Myers, Global Product Manager at nVent
Dana Myers is a Global Product Manager at nVent where she specializes in building product portfolio strategies to solve unique customer application challenges.
She makes an impact by developing and deploying new products and educating sales teams on how to best communicate and deliver the value-add to customers for the products she supports.
Dana entered as an industry specialist following a six-year career in the functional and process chemistry consulting industry.
After almost ten years at nVent, she has transitioned between several different roles and earned her MBA.